BACKGROUND
Mannville's Cornerstone Co-Op is part of a network of consumer cooperatives serving Northeastern Alberta, providing essential groceries, fuel, home supplies, and pharmacy services tailored to local communities. As
members, consumers have both ownership and governance rights within its democratic framework, playing a pivotal role in decision-making by electing a board of directors responsible for overseeing
operations and setting strategic goals. With a vested interest in operational efficiency, members directly benefit from the cooperative's success.
CHALLENGE
In the retail sector, the classic challenge lies in ensuring operational affordability, maintaining dependable equipment for service sustainability, and adhering to regulatory standards. In the Mannville
branch, an outdated refrigeration system with obsolete technology posed a significant issue, having exceeded its intended lifespan. Their legacy system, housed in the mechanical room, relied on 13 individual
compressors for refrigerated loads. They operated with static pressures and an on/off protocol that maintained maximum capacity regardless of requirements. The system's high-pressure design led to continuous
expansion and contraction cycles in refrigeration components, placing strain on mechanical and electrical parts. Their bills indicated significant energy use, but lacking a
management system to supervise operations, they couldn't accurately assess how their system was impacting profits. Faced with the operational hurdles of high energy consumption and rising repair costs, they were hesitant to invest in similar
equipment that would replicate the inefficiencies of their current system. They sought a scalable platform to ensure reliable equipment performance, improve efficiency, achieve cost savings, and align
with environmental objectives.
SOLUTION
The Co-op upgraded their outdated refrigeration system to the advanced automation of the Oxford Low Pressure Platform (OLPPTM). This transition involved integrating new condenser coils and
replacing the old compressors with 4 variable speed scroll compressors on an outdoor skid to serve retail cases, the walk-in cooler, and the freezer. The platform harnesses the advantages of low-pressure
refrigerants, advanced digital technologies and enables comprehensive system management through SensoriTM Building Automation System (BAS).
Diverging from conventional practices, digitalization, and the low-pressure design of the OLPPTM eliminate the need for high pressures to attain effective refrigeration. It operates with significantly lowered operating pressures and does not subject components to the wear and tear that shortens their lifespan. Electronic controls eliminate the need for conventional pressure differentials and leverage low compression ratios, which lowers discharge temperatures and minimizes secondary waste heat. Reduced compression ratios decrease the work required by the compressors, leading to a more responsive and efficient process that minimizes energy waste and reduces the overall impact of the system.
Comprehensive connectivity is crucial for a system's effectiveness. SensoriTM BAS digitally connects each device, allowing components to communicate and share crucial data to optimize performance. Compressor operation is fine-tuned according to ambient temperatures and load demands, eliminating the need for constant operation at maximum thresholds, which directly impacts energy demand.
The OLPPTM is engineered with supervisory control and data acquisition (SCADA) which allow the Co-op to control processes locally or at remote locations. Remote capabilities deliver instant notifications and the ability to act immediately to prevent issues, ensuring equipment durability and reliability. The Co-op has access to all relevant data, removing the guesswork and making it easier to manage and monitor the system.
RESULTS
Improving equipment performance with low pressure advantages and digital integration reduces energy use and promotes a sustainable approach to refrigeration.
Beyond environmental advantages, it's a financial win for system owners.
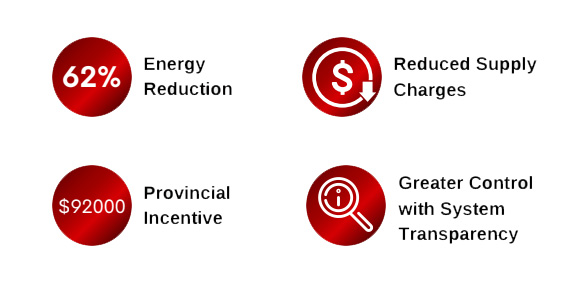
Sercon Refrigeration Ltd., a local commercial/industrial refrigeration & HVAC company, played a crucial role in swiftly installing the system with their expert team. Their skills, combined with the system's pre-programmed, plug-and-play format, significantly reduced downtime during installation and commissioning. SensoriTM management gives the Co-op a straightforward way to follow their refrigeration system's performance, offering insights into how it impacts both their business and environmental goals. They can easily monitor, understand, and adjust settings to boost performance, protect their system and save money in the long run. Their system includes a built-in energy meter that works like an independent device. Using Modbus communication, it meticulously tracks power usage for various components like compression, condenser, fans, and defrost heaters. Thanks to this setup, the Co-op slashed energy consumption by 62%, leading to a reduced commercial hydro rate and a significant $92,000 incentive from Alberta for cutting down on electricity use.
The digital transition with the Oxford Low Pressure Platform has not only helped the Co-op meet its environmental targets but also saved costs that can benefit members through lower prices or reinvestment in local programs. By opting for energy-efficient solutions, the Co-op isn't just tackling immediate operational issues but also showing a commitment to community values. This approach builds a more sustainable, resilient, and community- centered business, reflecting the Co-op's dedication to meeting the ever-changing needs and values of its members.
This project is part of Emissions Reduction Alberta Expanded Technology Pilot program. Read the final project report here.
